From prototype to full-scale manufacture
Lithium-ion batteries (LIB) are widely used as key rechargeable power sources for portable electronic devices.
When compared to other battery chemistries LIBs feature high energy densities, no memory effect, and a relatively low self-discharge when not in use. These advantages explain their rapid spread in the marketplace since their commercial introduction in the early 90s. Other growing applications for LIBs are from electric vehicles, and stationary energy storage devices where they are used to offset times of peak energy demand.
Overall, the market for LIBs is developing extremely rapidly and is currently expected to reach a $30-billion peak value by 2025. The main components of the LIB are anode, cathode, separator, and electrolyte. Very often the cathode material is a lithium transition metal oxide (e.g. LiMn2O4, or Li(NiMnCo)O2) which is the source of lithium ions. For the anode, graphite is often used as an active material.
During charging, the cathode is delithiated, where lithium ions move from the cathode through the separator to the anode and are intercalated into the carbon layers of the graphite. Each ion stores a certain amount of energy, which is retrieved during battery operation (discharge).
The lifetime and performance of the LIB are mainly determined by the constituent active materials and the microstructure of the active mass coating. In order to maintain battery life, it is important to measure and understand critical parameters such as particle size, shape and distribution, the presence of voids and defects within the particles, porosity, pore tortuosity, and coating thicknesses.
Mantec Technical Ceramics is involved in the manufacture of prototype battery cells and assists this industry sector through the development and integration of modern-day battery technology, from inception to full scale.
We are pleased to work in support of some leading, cutting-edge manufacturers.
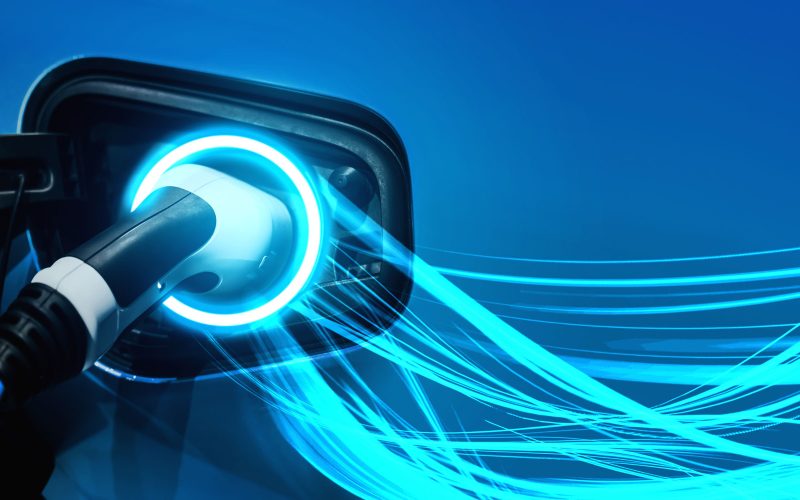